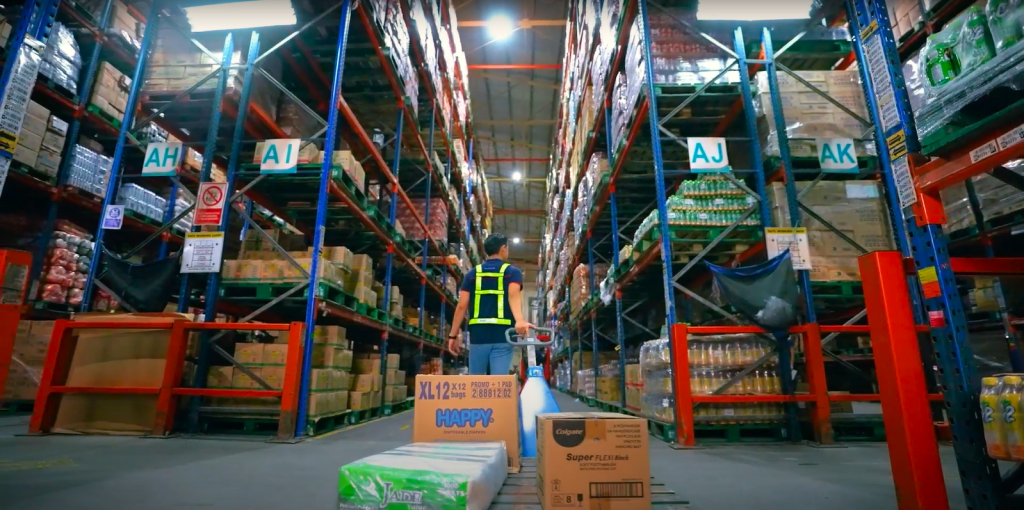
Inventory management challenges in small warehouse spaces pose serious challenges to the supply chain.
Limited storage capacity often leads to disorganization and overcrowding of inventory, making it difficult to locate items quickly and accurately. It can also cause potential stockouts or overstock situations, while delaying order fulfillment and deliveries.
Businesses should therefore adopt inventory management systems and effective solutions to address challenges in compact warehouses. By employing strategies to optimize space and manage inventory more effectively, businesses can enhance customer satisfaction, boost operational efficiency, and increase profitability.
FAST Logistics Group, the Philippines’ leading end-to-end logistics solutions provider, explores the challenges of managing inventory in small warehouse spaces and offers practical solutions to maximize available space and streamline supply chain operations.
Inventory Management Challenges in Small Warehouses Spaces
Small warehouses have limited storage space, which means every inch counts. This limitation poses various challenges that can hinder the smooth flow of operations and affect customer satisfaction. Among the disadvantages of small warehouse space are the following.
Stockouts and Limited Product Availability
One of the primary challenges in managing small warehouses is limited storage space. This restricts the amount of inventory and variety of products that can be housed at any given time, which causes stockouts.
Consequently, limited inventory can negatively impact customer experience and sales, particularly during periods of high demand. When customers are unable to find the products they need, it can lead to frustration and a negative shopping experience. This not only affects immediate sales but can also damage long-term customer loyalty and brand reputation.
Congestion and Disorganization
Small warehouse spaces frequently lead to overcrowding and disorganization primarily due to their limited physical footprint. With less room available for storage, shelves and aisles can quickly become congested as inventory accumulates. This overcrowding makes it challenging to maintain a systematic layout where items are well-organized and easily accessible.
Overcrowding and disorganization of inventory in small warehouses can significantly impact business operations. Inefficient storage practices also reduce overall warehouse productivity as warehouse employees spend more time searching for items or navigating overcrowded shelves and cluttered spaces.
Awkward Warehouse Layout
Small warehouses must make the most of every square foot. This often necessitates compromises in layout design, such as narrower aisles for more space or reduced spacing between racks to fit more inventory. These space-saving measures can lead to challenges like decreased accessibility, making it harder for business personnel to reach certain items.
Furthermore, it is more difficult to maneuver forklifts and other moving equipment within confined spaces. Such compromises can disrupt the flow within the warehouse, potentially slowing down operations, and increasing the risk of accidents.
Foregoing Automation
Small warehouses have constrained space, which may not accommodate large-scale automated systems effectively. Moreover, businesses with small warehouses may be cautious about the ROI of automation and expensive equipment, especially if they operate on tight profit margins.
Consequently, small warehouses are more likely to rely on manual processes, which are susceptible to inaccurate inventory information and human errors. Without automation, businesses suffer from inefficient warehouse operations and delays in order fulfillment processes.
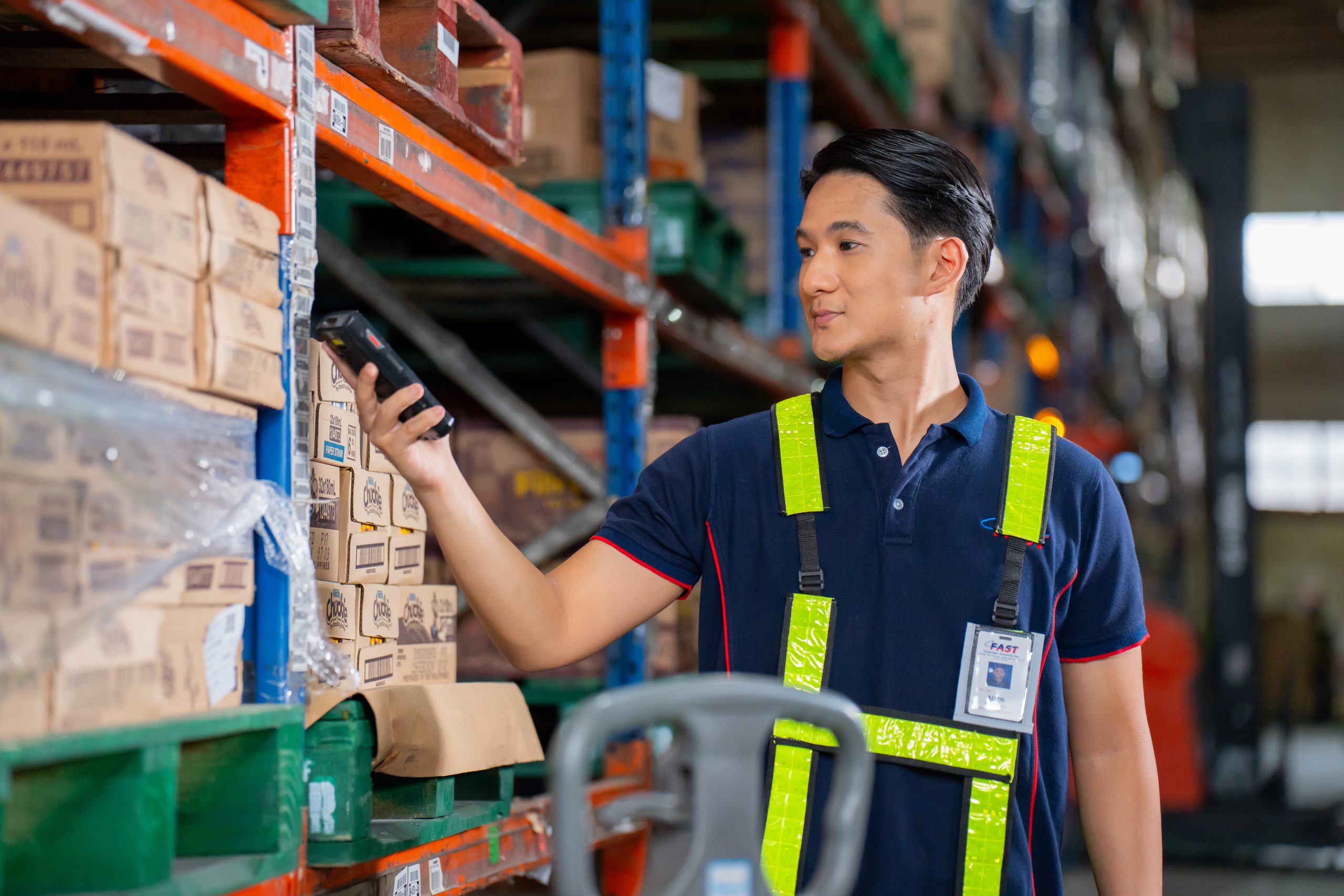
Warehouse Management System is used to streamline and optimize every stage of the warehouse processes. It offers comprehensive, centralized tools for managing various warehouse activities, including inventory management, order processing, picking, packing, shipping, and overall warehouse performance. With WMS, our clients across diverse industries benefit from real-time inventory tracking, order accuracy verification, workforce management, automated workflows, and seamless system integration.
Inefficient Picking Process
In small warehouses, the picking process is often manual and time-consuming. Limited space can hinder the implementation of modern inventory management systems and picking technologies, such as barcode technology and other automated tools. Additionally, compact warehouses may lack optimized layouts for efficient picking routes, forcing pickers to navigate cluttered aisles to retrieve items.
This inefficiency can result in longer lead times, increased labor costs, and a greater risk of human error, ultimately affecting the quality control, productivity, and profitability of warehouse operations and supply chains.
FAST also offers Voice Pick by FAST, a pick-by-voice solution powered by Honeywell. This technology enables quick and accurate order picking in warehouse or distribution center using voice commands. It enhances inventory accuracy, reduces shrinkage with real-time insights into order picking processes, and ensures faster picking times by allowing employees to focus on their tasks without constant interruptions. Additionally, it eliminates paper-based systems, reducing costs related to printing, filing, and storing paperwork.
Longer Order Fulfillment Times
Small warehouses often lack sophisticated order management and systems that provide real-time visibility into stock levels and locations. Instead, warehouse employees resort to manual processes like handwritten picking lists and manual inventory checks, which are more prone to errors. Manual methods delay the order fulfillment process, as employees search for items or update the inventory control for longer periods of time.
Additionally, small warehouses typically have smaller teams compared to larger facilities, leading to potential bottlenecks during peak periods or sudden spikes in order volumes. These factors delay picking, packing, and shipping orders, affecting fulfillment times and customer satisfaction.
Safety Concerns
Safety concerns arise in small warehouse spaces due to limited room for movement and storage. Overcrowded areas or cluttered aisles increase the risk of accidents and injuries, posing a significant threat to both employees and inventory, as well as potentially escalating labor costs.
Inadequate lighting, improper storage of hazardous materials, and insufficient safety training can exacerbate these risks. Implementing proper safety measures, such as regular safety audits, clear signage, employee training programs, and well-organized storage systems, is essential to create a secure work environment and ensure the well-being of all warehouse employees.
Inability to be Flexible and Adaptable
Because of limited space and technology, small warehouses often lack the flexibility to adapt to changing business needs or growth. Warehouse managers and employees struggle to accommodate larger volumes of incoming and outgoing inventory. In addition, they may not be able to implement changes in operational processes without significant reconfiguration during sudden increases in demand or seasonal fluctuations.
Moreover, small warehouses may face challenges in staffing during peak demand periods, as they may not have the flexibility to quickly hire and train additional personnel. This can exacerbate delays in processing customer orders.
Strategies in Boosting Warehouse Operations in Small Warehouse Spaces
Warehouse managers and supply chain professionals can overcome challenges posed by small warehouse spaces. They can adopt innovative solutions to boost warehouse management operations without the need to purchase additional properties or facilities. Here are some strategies that can be employed by businesses to maximize their use of limited warehouse spaces.
Optimize Vertical Space
One effective strategy is to optimize vertical storage. Warehouse managers of compact spaces can utilize tall shelving units and stackable storage containers for increased storage capacity within the same footprint. By utilizing shelving, racks, or mezzanine levels effectively, businesses can store more inventory without needing to expand horizontally, which can be costly in urban or constrained environments.
Maximizing vertical space also enhances operational efficiency. With better organization and layout, businesses can streamline workflows and reduce the distance traveled by warehouse employees to retrieve items. This efficiency is crucial in fulfilling customer orders promptly, especially when seasonal demand spikes.
Organize Warehouse Layout
Warehouse employees should designate specific areas for different types of inventory, such as raw materials, finished products, and packaging supplies. It is also important to use clear labeling and signage for easy identification and navigation.
Additionally, frequently accessed items should be positioned closer to the main aisles and loading docks to significantly reduce the time spent searching and picking items. Implementing a logical flow in the warehouse layout also minimizes potential errors and streamlines the whole warehouse management operations.
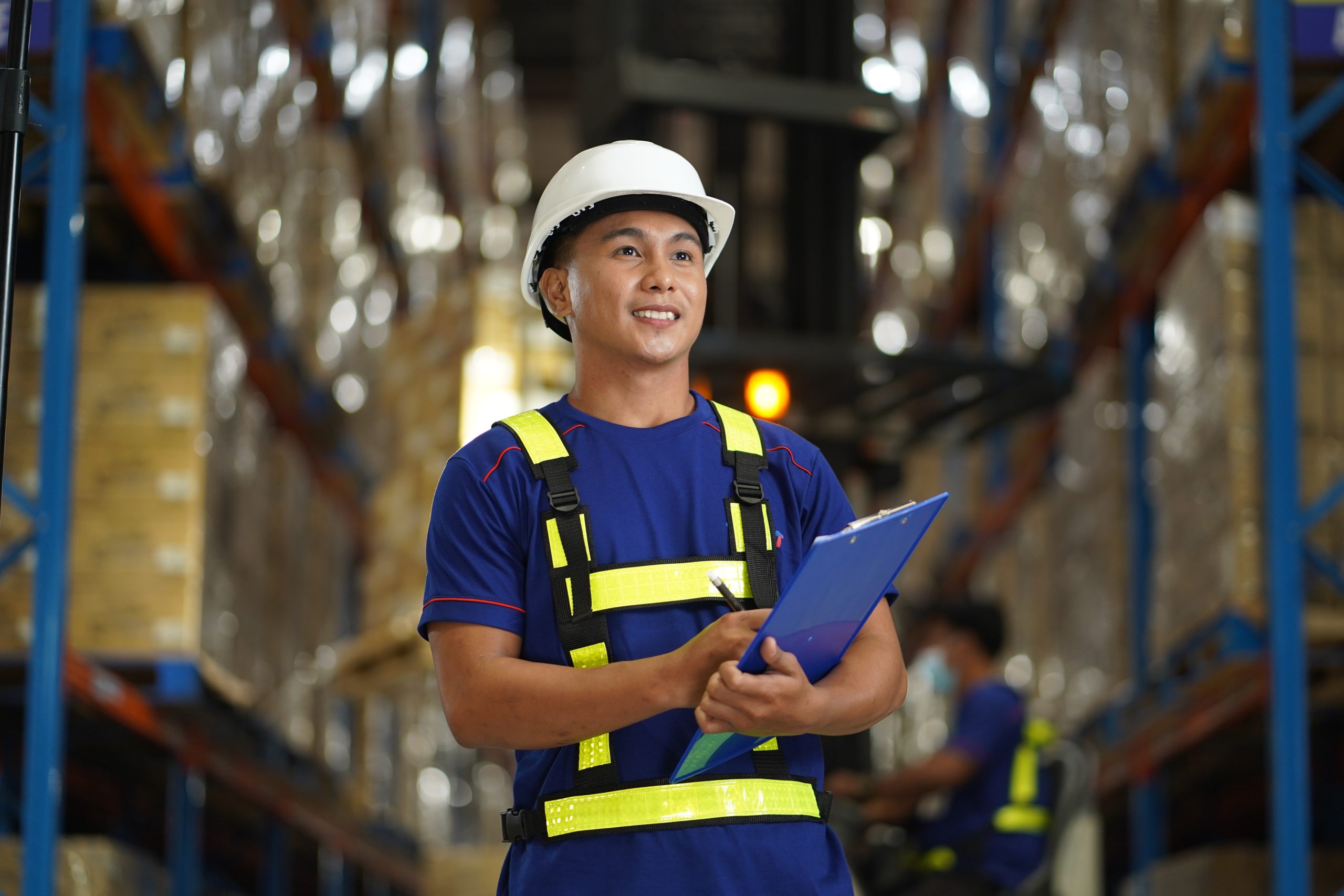
For forward-thinking companies ready to embrace a new era of industrial excellence, FAST offers comprehensive solutions to optimize warehouse operations and streamline supply chain processes.
Improve Accessibility with Aisle Markings and Signage
Clear aisle markings and signage are crucial for an organized and efficient small warehouse. Properly marked aisles allow warehouse personnel to quickly locate and access inventory, minimizing search time. They can also use color-coded markings and signs to designate different areas like storage zones, picking areas, and loading docks to enhance the workflow and minimize errors.
Regular updates and maintenance of markings and signage are necessary to reflect changes in layout and inventory. Periodic inspections help ensure that they remain legible and effective. Ultimately, investing in clear aisle markings and signage significantly improves accessibility and efficiency in warehouse and warehousing operations.
Invest in Compact and Modular Equipment
Narrow aisle forklifts, compact shelving systems, and stackable storage bins with a smaller footprint can be easily maneuvered in tight spaces. Businesses with smaller warehouses should invest in these tools and equipment to accommodate growing inventory levels without the need for costly expansions.
In addition, modular equipment offers flexibility and scalability. Equipment that can be easily reconfigured or expanded allows businesses to adapt quickly to changing operational needs and seasonal fluctuations in demand. This is particularly advantageous for small businesses that may experience varying inventory levels throughout the year.
Maximize Space with Mobile Shelving Units
Mobile shelving units are an adaptable storage solution that maximizes space in small warehouses. These units can be moved and adjusted to create various configurations. Investing in high-quality mobile shelving helps businesses increase storage capacity and be more flexible in arrangements.
Warehouse managers should regularly assess their shelving layout to match changes in inventory levels and product types. This will also help in ensuring optimal use of available floor space throughout the warehouse.
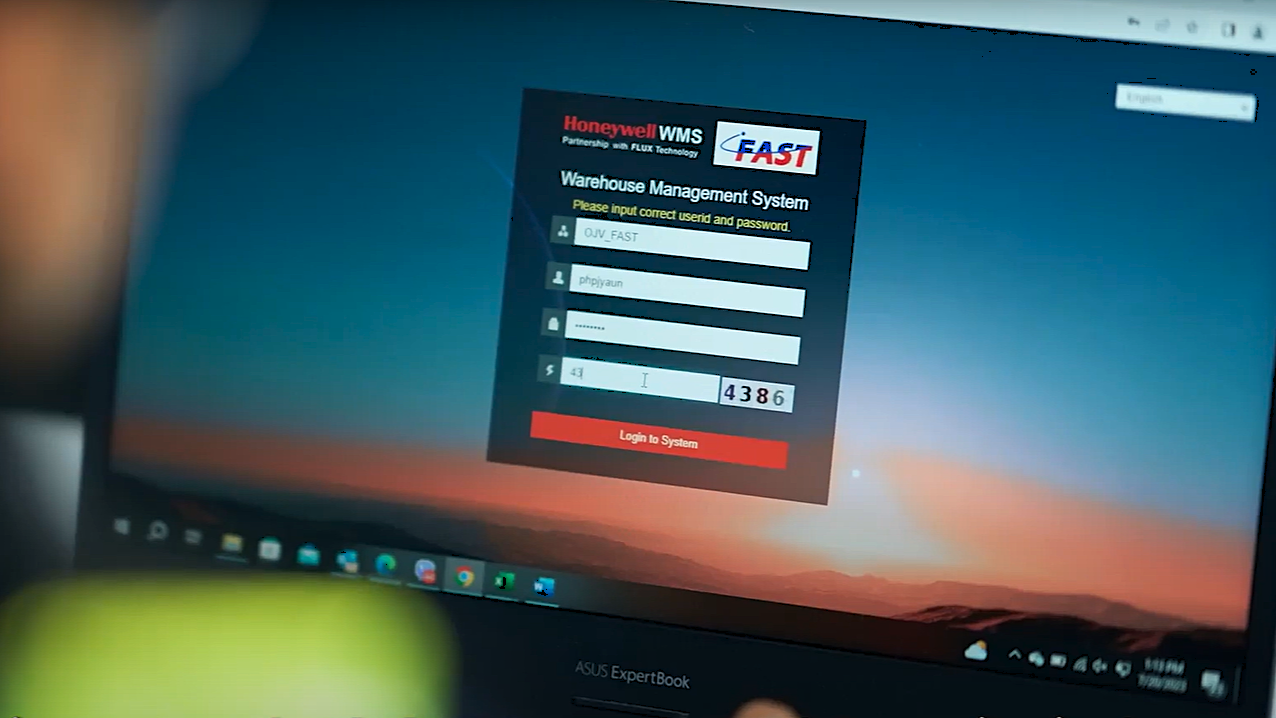
Implement Warehouse Management Software
To enhance efficiency in a small warehouse, businesses can utilize warehouse management software is crucial. These systems provide real-time tracking of stock levels, streamline order processing, generate detailed reports, and help address other warehouse management challenges. This technology also reduces the risk of overstocking or stockouts and provides real-time visibility for better decision-making.
Businesses should choose software that suits the size and complexity of their operations. Look for features such as barcode scanning, automated reordering, and integration with other business systems. These functionalities can significantly improve accuracy and productivity of warehouse processes.
Utilize Just-in-Time Inventory Management
Another solution in limited warehouse space is just-in-time (JIT) inventory management. This inventory strategy focuses on receiving goods only when they are needed for production or sales. It minimizes the amount of inventory held in storage, freeing up valuable space in compact warehouses.
Implementing JIT requires close collaboration with suppliers to ensure that materials and components arrive exactly when needed. Establishing strong relationships and clear communication channels with suppliers, as well as precise planning and monitoring, are essential to make this strategy work. Businesses should regularly review and adjust their JIT processes to adapt to changing demand patterns and supplier capabilities.
Adopt Cross-Docking Techniques
Cross-docking is a logistics strategy that involves directly transferring incoming goods to outgoing shipments without storing them in a warehouse for a long time. Notably, this technique is especially beneficial for fast-moving consumer goods or perishable products, as it maintains product quality and freshness.
In addition, cross-docking reduces storage needs and accelerates the cash flow out of goods through the supply chain. Implementing cross-docking can also significantly improve the efficiency of a small warehouse by streamlining operations and reducing handling time.
Leverage Dropshipping Partnerships
Dropshipping is a fulfillment method where products are shipped directly from the supplier to the customer, eliminating the need for physical inventory storage. By leveraging dropshipping, businesses can track inventory and offer a wide range of products without the burden of storing it in a physical space. It is also a cost-effective way to grow the business.
Collaborating with reliable suppliers is essential to ensure quality standards and timely deliveries, which helps maintain customer satisfaction. Regularly reviewing supplier performance and seeking feedback from customers can further enhance the overall dropshipping strategy.
Enhance Efficiency with Lean Inventory Practices
Lean inventory practices aim to minimize waste and maximize efficiency in warehouse operations through continuous improvement and the elimination of non-value-added activities and obsolete inventory. By conducting a thorough analysis of current processes and implementing standard operating procedures, businesses can streamline tasks, reduce variability and errors, and optimize warehouse space for better performance.
Supply chain leaders should inform and engage warehouse personnel about lean transformation processes. Provide training, encourage feedback, and empower employees to suggest improvements and take ownership of their work. A collaborative and continuous improvement mindset can greatly enhance the efficiency and overall performance of small warehouse spaces.
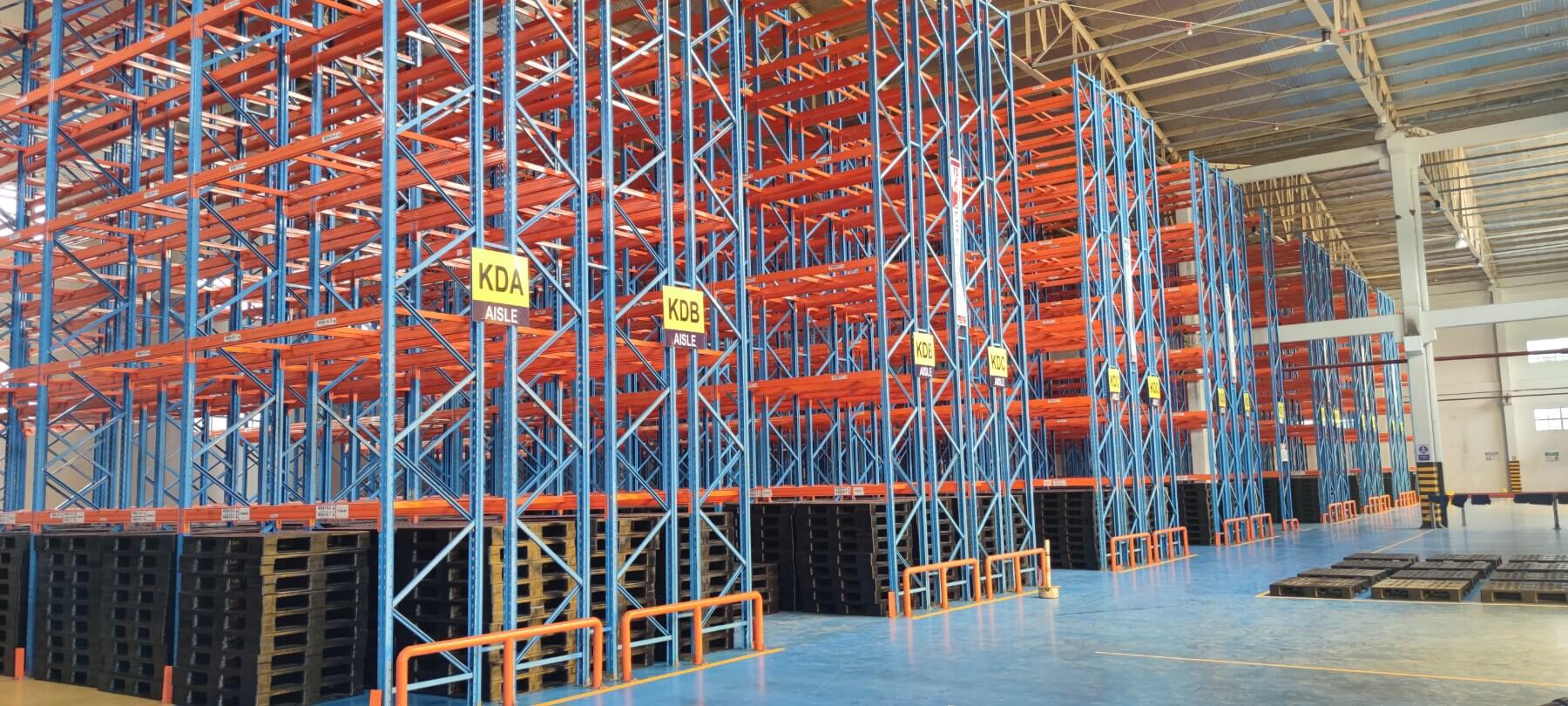
With Space by FAST, businesses can lease our strategically located warehouse spaces for maximum efficiency and success. These are located in Calamba and Cabuyao in Laguna; Meycauyan in Bulacan; and Kalawaan in Pasig.
Lease Multiple Warehouses
Another practical solution to address space constraints is leasing additional warehouse spaces. This option allows companies to expand your storage capacity without the long-term commitment of purchasing property. Leasing provides flexibility to scale up or down based on business needs.
When selecting a leased or warehouse location, consider important factors such as location, accessibility, and rental terms. Proximity to main hubs can reduce transportation and fuel costs. Ensure the lease agreement aligns with budget and long-term plans.
Leased spaces can also offer amenities such as security, climate control, and loading docks, enhancing the overall functionality of storage facilities. This solution provides a cost-effective way to manage excess inventory and accommodate seasonal demand fluctuations.
Rent a Shared Warehouse Space
One innovative and cost-effective approach is to rent a shared warehouse space. Shared warehouses, also known as co-warehousing, involve multiple businesses sharing a single facility. This arrangement can significantly reduce costs while providing access to larger and better-equipped spaces.
Shared warehouse spaces often come with added benefits such as shared staffing, equipment, and services. This collaborative environment fosters networking opportunities and knowledge sharing among businesses. It’s a win-win situation to save money and gain valuable insights.
When considering a shared warehouse, evaluate the compatibility of your business with potential co-tenants. Ensure that their operations and storage needs align with yours to avoid conflicts. This solution is ideal for small businesses looking to optimize their storage capabilities without investing heavily in infrastructure.
Innovative Approaches to Warehouse Management Challenges
Effectively managing inventory in a small warehouse space requires innovative approaches and a proactive mindset. With meticulous organization and regular operational audits, businesses can effectively optimize limited warehouse space while improving the overall quality control efficiency of their warehouse management processes.
Companies can optimize vertical storage, leverage technology, and adopt strategies like just-in-time inventory and dropshipping to overcome the warehouse challenges posed by small warehouse space. Enhancing efficiency with lean practices, mobile shelving, and clear aisle markings will further maximize their warehouse potential.
Furthermore, leasing additional warehouse space or renting shared spaces can provide the flexibility needed to accommodate growth, especially during peak seasons or periods of increased demand. This approach allows businesses to scale their operations without the long-term commitment of purchasing property, and can also offer access to technology, better facilities, and strategic locations that might otherwise be out of reach.
FAST Logistics Group, the leading provider of end-to-end logistics solutions in the Philippines, offers premium industrial space solutions tailored to meet the diverse needs of companies like yours. With more than 50 years of industry leadership, FAST possesses the expertise, capabilities, and technology to help your business flourish in a competitive market.
Don’t let limited warehouse space hold your business back. Learn more about our end-to-end logistics solutions through our Solutions Experts. You may also visit http://linktr.ee/fastlogisticsph today
Categories
-
FAST Ahead
Includes case studies and testimonials of our partners as well as other featurettes from industry experts
-
FAST Hacks
We simplify logistics terms and provide practical tips and solutions for the DIY in you
-
FAST Highlights
Know more about our history, various brands, achievements, and news updates
-
FAST Moments
Get to know the people of FAST, our employee programs, as well as our various ways of giving back to the community
-
FAST Solutions
Learn more about the various logistics solutions that we cater to and offer our clients, as well as tech innovations, and service facilities