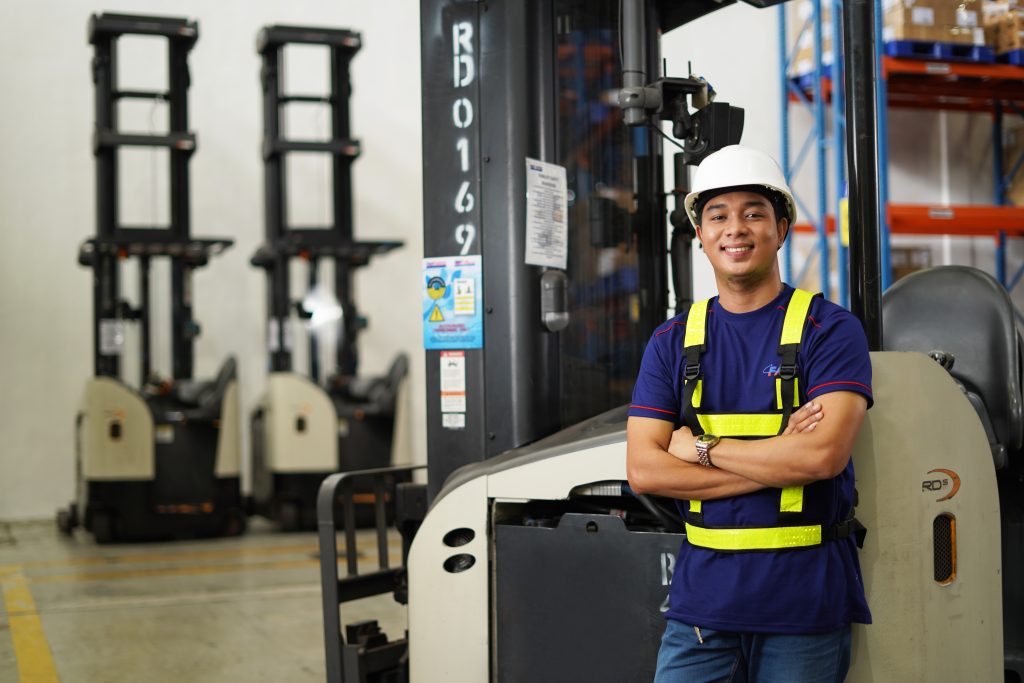
FAST Logistics Group, the leading end-to-end logistics company in the Philippines, tackles the significance of integrating technology in warehouse and transport operations to enhance workplace safety in logistics.
Safety in the workplace is crucial in any industry, but it is especially vital in the logistics sector where employees are constantly exposed to dangers. Using heavy equipment, handling hazardous materials, and working at heights or on the road pose risks for workers involved in warehouse and transport activities. Strengthening safety measures should therefore be a top priority for any logistics company to prevent accidents that can endanger lives, derail supply chain operations, and compromise customer products.
With technology, logistics providers can adapt and incorporate innovation into their processes. This not only improves efficiency, accuracy, and productivity but also maintains worker safety. Hence, supply chain managers should leverage technology to have a safer, more efficient work environment.
What is Workplace Safety in Logistics
Workplace safety in logistics refers to the measures and practices implemented to protect employees from safety hazards in warehouse and transport operations. It encompasses safety measures to ensure employees are free from accidents and injuries.
Safety, in this context, is both a right and responsibility of everyone involved — one that protects not only the workers but also the integrity of the supply chain on which countless industries depend. Logistics managers should thus take the lead in implementing safety initiatives in their operations, from identifying potential safety risks, providing appropriate employee training, and enforcing procedures for the health and safety of their employees.
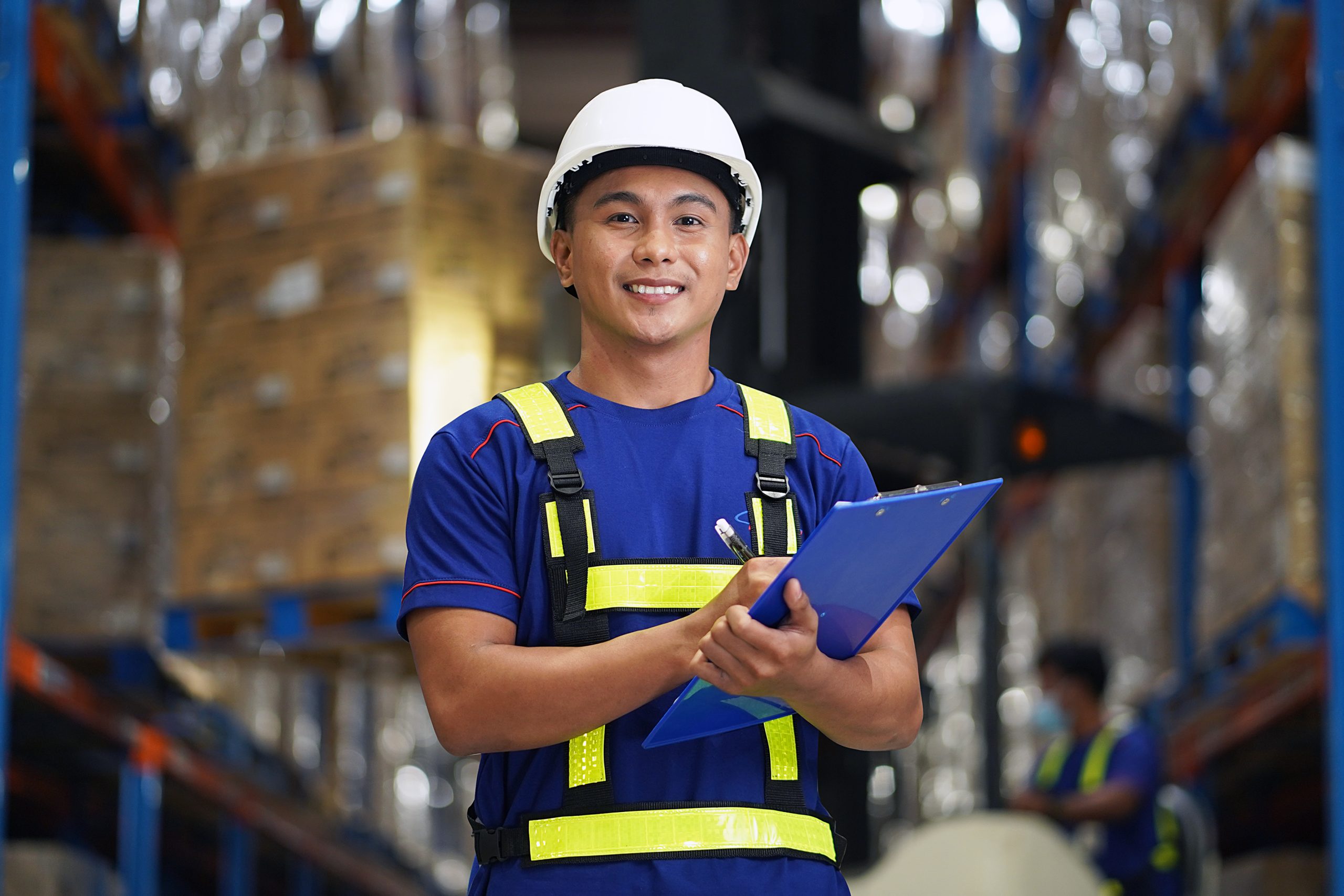
What Factors Affect Workplace Safety in Logistics
Warehouse and transport operations involve dynamic, demanding, and fast-paced activities that require focus, agility, coordination, and communication. The complexity of logistics operations can increase the risk of workplace accidents and injuries. Here are some factors that can affect workplace safety in logistics.
Machine and Equipment
Logistics operations rely heavily on machinery and equipment, such as forklifts, cranes, conveyors, pallet jacks, and delivery vehicles. These machines have the potential to cause severe injuries if not used properly or maintained regularly. Workers operating these machines must be trained well to ensure the safety of those involved in the supply chain process.
Nature of Materials
Logistics operations involve handling different types of goods, including hazardous materials that require special attention and care. The nature of the materials being handled, stored, and transported — which involves their weight, size, or toxicity — defines the safety controls needed for proper handling within the logistics environment. Every employee must be knowledgeable about the proper handling of such materials to prevent accidents in the workplace.
Method or Procedures
The diverse range of tasks and processes in logistics operations must be carefully planned and executed to ensure safety. This includes proper loading and unloading, storage, and transportation of goods. Employees must strictly follow these procedures to protect themselves and others from harm.
Physical Environment
The layout and design of the warehouse and transport areas can also impact workplace safety. Narrow aisles, cluttered spaces, or slippery surfaces might lead to accidents such as slips, trips, and falls. Workplaces must be conducive for work and potential hazards that may cause injury to employees should be removed.
Personal and Job Factors
Workplace safety in logistics is also influenced by personal and job-related factors. For instance, employee behavior and level of stress significantly influence their ability to work safely. It is therefore essential for employers to promote a positive work culture that prioritizes employee health and well-being. Awareness, training, and experiences will also help them prevent accidents or respond correctly in case crises occur.
What are Common Safety Issues in Logistics
The logistics industry faces various challenges when it comes to ensuring workplace safety. Here are some of the most common safety issues in logistics.
Physical Hazards
Physical hazards are dangers that can harm a person’s health or safety, primarily caused by machines, equipment, and materials used in logistics operations. These hazards include falling objects, uneven flooring, slippery surfaces, or cluttered work areas. Handling heavy machinery and equipment also poses a risk of crush injuries or being caught in between moving parts. Moreover, exposure to hazardous materials such as chemicals or fumes further contributes to the physical risks faced by workers in logistics environments.
Vehicle Accidents
The significant number of fleet vehicles in logistics operations raises safety concerns, including collisions and overturns. Accidents may happen on the road, at loading docks, or inside warehouses due to insufficient training, driver fatigue, poor maintenance, or distracted driving. These issues can result in serious injuries or fatalities among workers, emphasizing the importance for logistics firms to prioritize safety.
Hazardous Chemicals
Another common issue in workplace safety involves handling and transporting dangerous materials. Without proper management of storing and transporting hazardous materials, workers are at a higher risk of fires, explosions, or exposure to toxic substances. Proper training and compliance with safety regulations are essential in minimizing the risks associated with such materials.
Ergonomic Risks
The physical demands of logistics operations, such as frequent lifting, carrying, and bending, can lead to ergonomic risks. These include musculoskeletal disorders and repetitive strain injuries that have long-term health complications for workers. Employers must provide ergonomic training and implement measures such as proper lifting techniques and equipment to mitigate the impacts of these risks.
Lack of Training and Education
A workforce that is unaware of or untrained in the potential risks of their work environment will be less equipped to mitigate safety hazards effectively. Lack of training and education can also lead to accidents, injuries, and even fatalities. Therefore, regular safety training should be a priority for logistics companies to ensure their employees are equipped with the necessary knowledge and skills to protect themselves, their co-workers, and the products they are handling.
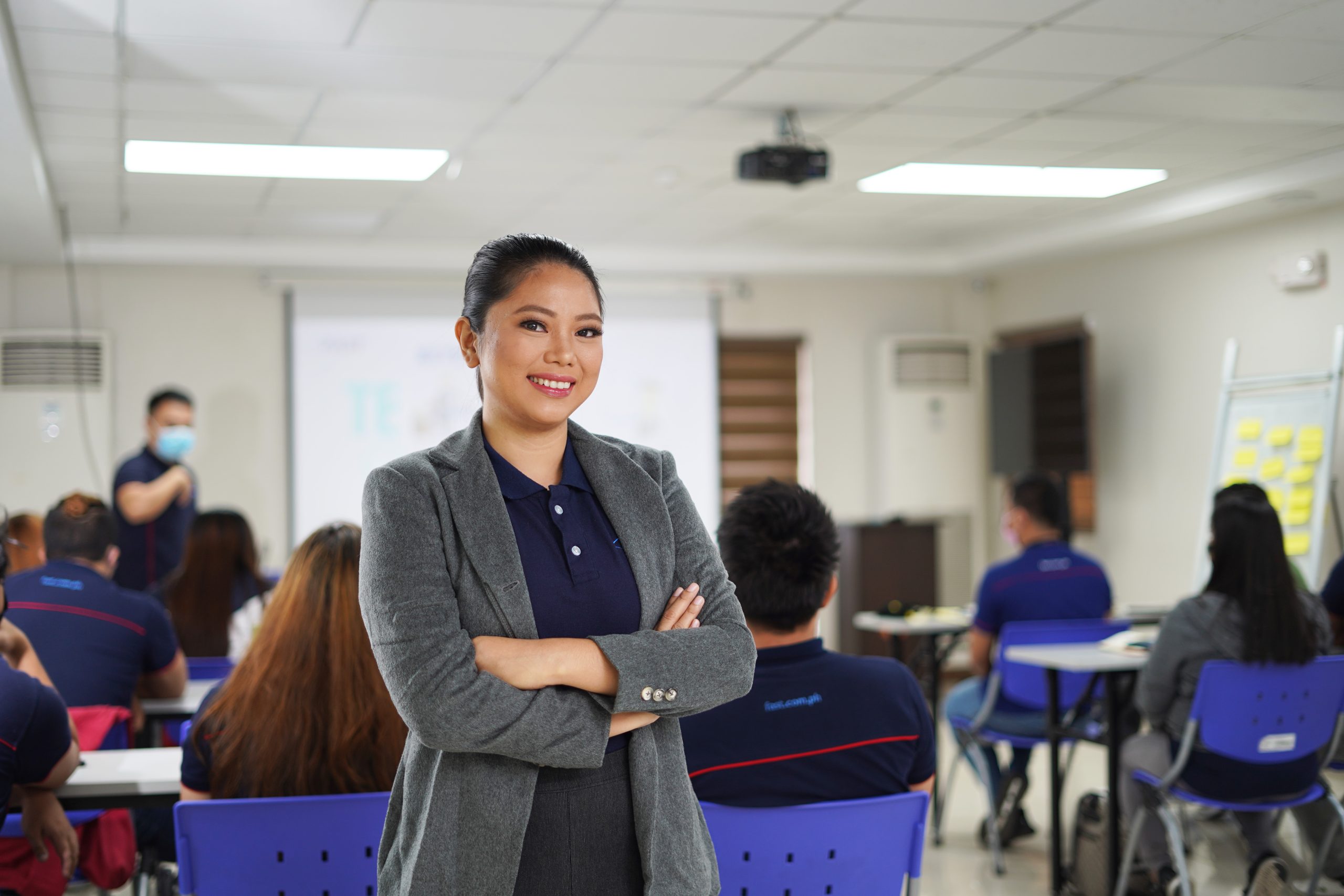
How to Approach Workplace Safety in Logistics
To encourage a safety-first culture in logistics, companies must adopt both preventive and reactive approaches that will enable them to eliminate hazards before accidents can occur and respond to emergencies in a timely manner.
Preventive Measures
Implementing preventive measures is crucial to reduce the risk of accidents and injuries in logistics. These can include conducting regular safety audits and proper maintenance of equipment and machines. Regular safety meetings to assess safety performance can also serve as a platform for employees to ensure they are aware of potential hazards and equipped with the skills needed to mitigate risks. Enforcing safety procedures and updating safety measures are also essential in preventing accidents.
Reactive Measures
In addition to preventive measures, logistics companies should also be prepared to respond promptly to any potential safety issues. This can include having emergency plans and procedures in place for different scenarios such as fire or explosion and conducting regular drills for emergency situations. Having well-defined procedures for incident response, a clear line of reporting, and provision of first-aid are vital reactive measures during unforeseen events. Reporting and investigating incidents can also help to identify gaps in safety protocols and address them promptly.
Ultimately, a balanced approach that affords equal priority to both types of measures will lead to improved safety outcomes.
What are Technological Innovations Improving Workplace Safety in Logistics
Apart from the aforementioned approaches, technological advancements also play a significant role in improving workplace safety in logistics. Companies might not realize that the innovations they implement to enhance operations and streamline processes can also significantly improve workplace safety. Some examples of such technologies are the following.
Warehouse Management System
Software systems used to monitor all warehouse processes, which are also referred to as Warehouse Management System, easily automate inventory levels, order fulfillment, and product movements. By automating these processes and reducing the need for manual labor, companies can minimize the risk of worker injuries. Moreover, WMS also helps to optimize warehouse layout and workflow, preventing workers from having to navigate hazardous conditions.
FAST Logistics Group, which has the largest warehouse footprint in the country, is also the Philippines’ first and only implementer of a Warehouse Management System powered by Honeywell. Businesses can make use of this sophisticated software solution to enhance their overall operational efficiency.
Safety Sensors and Alarms
Implementing sensors and alarms at strategic points within warehouses and logistical centers significantly enhances safety by identifying potential hazards. For instance, utilizing temperature sensors helps avert fires while motion sensors can be used to avoid unauthorized access to restricted zones.
Drones for Inspections and Surveillance
Drones equipped with cameras can be used to inspect high-risk areas in warehouses or monitor large outdoor facilities, reducing the need for workers to manually carry out these tasks. This minimizes the risk of falls and other accidents that may occur during inspections. Drones can also be used for surveillance purposes to monitor the movement of vehicles and personnel, detect potential hazards, and respond promptly in emergencies.
Fleet Tracking and Monitoring Systems
Logistics providers that leverage real-time tracking systems to regularly monitor their fleet vehicles, driver behavior, and delivery status can quickly identify potential safety violations. These systems provide a real-time view of vehicles’ locations and speeds, helping companies take proactive measures to prevent accidents. Moreover, monitoring driver behavior can also ensure compliance with safety protocols such as wearing seatbelts or avoiding distracted driving.
FAST Logistics Group, which operates the largest vehicle fleet in the Philippines, has been using GPS and AI Dashcams in its vehicles to track and monitor driver behavior and record critical incident data for post-accident analysis and learning. Watch the video below to learn more.
Smart Personal Protective Equipment (PPE)
Technological advancements have paved the way for the creation of personal protective equipment (PPE) equipped with innovative features like integrated microphones, cameras, and sensors. These enhancements are designed to warn both workers and supervisors about potential hazards or incidents, thereby elevating safety measures and ensuring swift action during emergencies.
Virtual Reality
Virtual reality technology empowers employees with the skills to navigate real-life situations through immersive, simulated training environments without exposing them to actual dangers. This cutting-edge approach is invaluable for mastering the operation of heavy machinery and the safe handling of hazardous materials.
Exoskeletons
Exoskeletons, as wearable robotic suits, offer support and assistance to workers engaged in physically strenuous activities. These suits play a crucial role in minimizing the risk of musculoskeletal injuries and fatigue, particularly in logistics operations characterized by heavy lifting and repetitive tasks.
Smart Lighting Systems
Lighting systems, when outfitted with sensors and timers, offer a smart solution for warehouses and similar facilities. These systems adjust lighting levels based on occupancy, leading to significant energy savings and enhanced safety by ensuring adequate illumination across all areas.
Technological innovations continue to evolve and offer numerous opportunities for logistics companies to enhance workplace safety, making it a crucial aspect of operations that should not be overlooked. Companies must continually adapt and integrate these advancements into their safety protocols to ensure the well-being of employees.
What are the Benefits of Enhancing Workplace Safety in Logistics
Safety must be considered a mission-critical aspect of the logistics industry. Not only does it protect employees from harm and businesses from operational disruptions, but it also enhances the overall efficiency and reputation of the supply chain. Here are some of the key benefits of adhering to safety guidelines in logistics.
Reduced Accidents and Injuries
Adhering to safety processes can significantly reduce the number of accidents and injuries. This not only protects employees but also reduces the potential for costly workplace disruptions and legal issues. It also results in reduced expenses associated with damaged equipment or goods.
Improved Employee Morale
Employees who feel secure in their working environment are more likely to be more engaged and productive. Reducing accidents and the associated downtime through preventative tech-driven measures can also have a significant positive impact on the bottom line.
Fewer Supply Chain Disruptions
In the face of an incident, a robust safety culture and technology-backed responses can ensure swift and efficient recovery, leading to minimal disruption in the supply chain. This prevents delays and financial losses, making logistics operations more reliable for customers.
Enhanced Reputation and Competitive Edge
Ensuring workplace safety not only protects employees but also enhances a company’s reputation as a responsible and ethical business. This can lead to an improved competitive edge in the market, attracting top talent and building trust with customers.
Encouraging Workplace Safety in Logistics Through Innovation and Technology
Adopting innovation in logistics safety doesn’t just rest on the shoulders of business executives and safety managers alone. Every employee should champion a safety-first culture by becoming familiar with the available tools and best practices. This collaborative approach will not only reduce the occurrence of workplace incidents but will also foster an environment where safety is a top priority.
Investing in technology and innovation in safety protocols can lead to long-term benefits for both employees and businesses in the logistics industry. It is crucial for companies to continuously evaluate and upgrade their safety measures to keep up with changing circumstances and evolving technologies.
With over 50 years of industry leadership, FAST Logistics Group is the leading end-to-end logistics company in the country that offers a comprehensive range of warehouse and transport solutions. To learn more about our services, contact our Solutions Expert or visit linktr.ee/fastlogisticsph
Categories
-
FAST Ahead
Includes case studies and testimonials of our partners as well as other featurettes from industry experts
-
FAST Hacks
We simplify logistics terms and provide practical tips and solutions for the DIY in you
-
FAST Highlights
Know more about our history, various brands, achievements, and news updates
-
FAST Moments
Get to know the people of FAST, our employee programs, as well as our various ways of giving back to the community
-
FAST Solutions
Learn more about the various logistics solutions that we cater to and offer our clients, as well as tech innovations, and service facilities